Development of python tools on Abaqus software_
Or the automation of a process instead of humans !
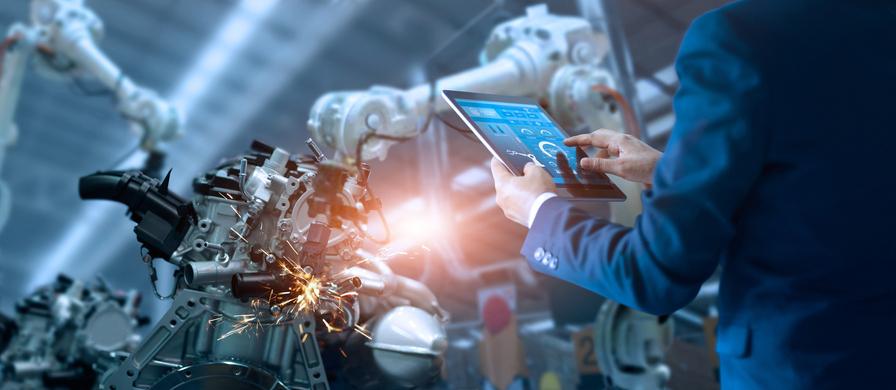
The context_
Our client, GTT, uses the Abaqus software, which makes it possible to perform digital model simulations using the finite element method.
Our client’s “structural calculation” center encounters a large number of studies with particularly heavy and complex post-processing, in particular in order to validate certain standards, sometimes severe, on various criteria. These post-processings, carried out manually until now, are mainly time-consuming.
It is in this context that the OSE team has developed 3 tools in python to post-process the calculations automatically:
A tool dedicated to the automatic export of images.
A stress averaging tool that analyzes a structure in order to validate certain criteria.
A tool for automatic detection of welds from a structural mesh.
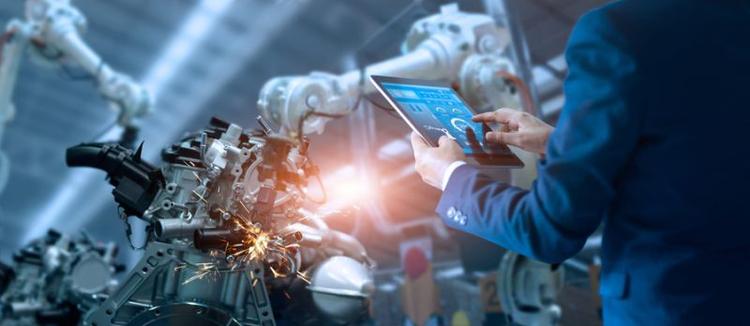
Python tools developed_
The Abaqus Viewer tool
Our Abaqus Viewer tool generates a large number of images to automatically produce our client’s reports. This tedious and recurring task was previously carried out manually.
We proposed a graphical interface in python Qt which allows to preconfigure all the post-processing to be performed in order to automatically generate the requested images.
Our solution takes into account pre-established configurations for certain types of post-processing that are regularly performed. Thanks to these configurations, the tool makes it possible to generate a hundred images in a very limited time, of the order of a minute.
The Mean Stress tool
Our Mean Stress tool aims to automate a particularly laborious task to be carried out manually: the verification of all the criteria defined by the classification societies (LR, ABS, DNV, BV, etc.).
The calculation of these criteria is based on the local averaging of the stresses exerted on the structure. The tool automatically performs these calculations, checks whether the criteria are validated or not and generates a report of the results to the user.
Different criteria and different methods can be used during this post-processing allowing a much more complete scanning of the study than what can be done manually.
The Weld Detection Tool
From a mesh of a structure, our Weld Detection tool automatically extracts all the edges that represent the welds in the structure and classifies them into different groups in order to prepare fatigue studies. We have proposed an innovative algorithmic method based on the construction of a graph to extract these welds.
To perform this extraction, our method goes through several steps:
Step 1 – We determine the adjacent meshes, i.e, the meshes sharing a common edge.
Step 2 – Calculate the angle between each pair of adjacent stitches.
Step 3 – We build a graph: each mesh represents a node of the graph, and two nodes of the graph are linked if the pair of meshes has a common edge.
Step 4 – We establish a form of connectivity according to the angle thus allowing us to extract all the substructures that make up the mesh.
Step 5 – Finally we detect the welds which are at the intersection of these substructures, and classified according to their geometric specificities.
The team developed in python both the algorithmic methods to efficiently post-process the results and also an ergonomic graphical interface.
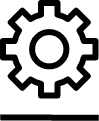
Benefit of the OSE solution_
The tools developed have made it possible to facilitate and automate our client’s work.
The benefits are as follows :
Significant time savings
Reliability of results
Co-development with the computing division of
structure of GTT
